Upset Management Engineer: Process Upsets Detection & Troubleshooting
Introduction:
Process upsets are among the most critical operational challenges faced by engineers in manufacturing, petrochemical, and other industrial sectors. Such upsets can lead to reduced efficiency, increased operational risks, and higher maintenance costs. Therefore, early detection of upsets, root cause analysis, and effective resolution skills are essential for any engineer.
This course aims to equip participants with the knowledge and tools required to monitor industrial processes, diagnose the root causes of upsets, and implement effective solutions to prevent recurrence, thereby enhancing operational efficiency and ensuring continuous production at the highest standards of safety and quality.
Who Should Attend:
- Process engineers in plants and industrial facilities.
- Operations and control engineers.
- Maintenance and technical support engineers.
- Leaders of operations teams and control room supervisors.
- Performance optimization engineers.
- Production managers and industrial facility supervisors.
- Any professional seeking to enhance their skills in fault detection and operational troubleshooting.
Course Content: Day 1: Introduction to Process Upsets
Day 2: Early Detection Techniques for Upsets
Day 3: Root Cause Problem-Solving Methodologies
Day 4: Solutions and Strategies for Handling Upsets
Day 5: Continuous Evaluation and Development
|
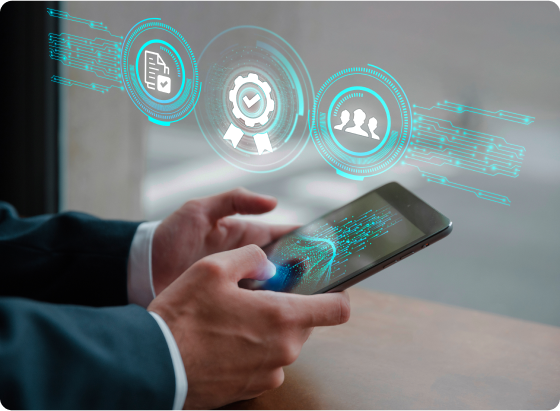
Upcoming Courses
BOOSTING GAS FLOW EQUIPMENT AND OPERATIONS




The Training Course:
Technical, Oil, and Gas ProgramsCONSTRUCTION PROJECT ADMINISTRATION & SITE MANAGEMENT




The Training Course:
Technical, Oil, and Gas ProgramsProcess Engineer: Reactor Operations, Troubleshooting, and Startup/Shutdown

